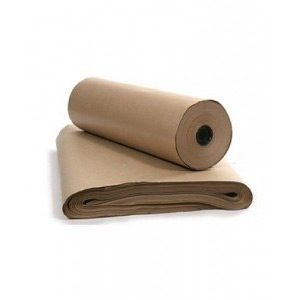
Kraft Paper
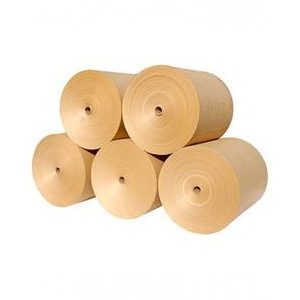
Absorbent Kraft Paper
Process:
Raw Material – Waste Paper, imported Waste Paper
Fuel – Pet Coke / Bagasse / Fire Wood
Chemical – Alum and Rosin
Packing Material – By Packing machine
Manufacturing process of Kraft Paper
Pulp Mill section
We are going to make fresh paper from waste paper viz corrugated boxes, paper cutting, waste paper sheet as a raw material which may be called as recycled fibers.
In the Process we take our shorted material in a spherical high density pulper through converyor system, back water (used water) is being added to it and the slurry is being rotated approx half an hour to make pulp, also stem is being taken to warm-up pulp slurry to ease fiber bonding.
The prepared batch of pulp is then taken out though pulp line and value to pulper pit from where the pulp material goes to screening system like jonson screen, Turbon separator in low consistency. The out let pulp from Turbo screen is being thickened in Decker Thickener and being collected in to the chest called a refining chest and then this pulp is being feed by a pump to refiner machinery where fibers are treated to get the desired paper property like bursting strength, tensile strength. Double fold surface texture etc and for water penetration(sizing of paper) is being controlled by addition of Rosin and Alum in the mixing chest.
The Prepared pulp is being collected in two nos. of machine chests from there this pulp stock is supplied to paper machine department.
Paper Machine Section
The pulp coming from the machine chest though stock regulating box goes to fan pump with lower consistency is being fed to centricleaner system from the cleaned accepted stock again goes to another elaming screen named Pressure Screen.
Now Pressure screen out let pulp stock goes to wire part head box and then stock pulp slurry is being spreaded over continuous synthetic wire cloth where water is being sucked out by the no of draining elements equipped with the water table.
The wet paper web then goes by the help of synthetic felt from wire part to press part where papersheet is being passed between two no’s of heavily loaded rolls to remove out excess water content of the sheet mechanically then after the sheet moves steam heated over the MG cylinder and paper sheets get dried with wined over pope reel in a tambour roll. Its continues process when paper roll get sufficient diameter it is being taken and another empty shell is being put to start wrapping the paper over pope reel.
Rewinder Section
The paper roll prepared from paper machine is being cut into party order size and dia on rewinder machine where big paper roll is being cut into small size reels
The reels are then weighted properly marked for grammage, size and weight and then wrapped with HDP covering, properly stitched and packed.
Now this final product will be ready to dispatch after commercial formalities.